OSHA Compliance for Nursing
Staff Inside The Nursing Home
By Bob Singer, BS, NHA, PCHA, Copyright
08/1998, Revised 02/2000
What is OSHA?
OSHA is the federal government's Occupational Safety and Health Administration. They are responsible for insuring compliance with federal regulations regarding occupational safety and workplace procedures. They are government inspectors, so they have rights to enter and investigate a work place with little or no prior notice. These inspectors do have the ability to institute fines and legal proceedings should they come across serious violations. In the past, OSHA primarily concentrated on the manufacturing industries, but in the last few years they have been surveying other fields including healthcare facilities. They are looking for safety hazards. They also examine the programs that the employer has established to prevent and keep track of accidents. By law, all major employers must have programs in place to comply with OSHA standards. Some of the key points to these programs include, but are not limited to Eye Wash Stations, easily accessible MSDS Sheets , Lockout-Tagout Equipment, Personal Protective Equipment (PPE) , Blood Spill Kits, Mercury Spill Kits, Incident Reporting Procedures, and a Master OSHA Control Log.
Specifically, what are these safety precautions? How does this effect the individual employee?
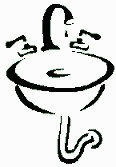
Eye Wash Stations
Eye Wash Stations are areas where an employee can wash out his or her eyes with clean water after foreign objects or chemicals have found their way into his or her
eyes. Eye Wash Stations can be permanent, such as a permanent attachment
onto a sink or they can be mobile, such as a fresh bottle of sterile water,
which can be used to flush one's eye while in transport to get more qualified
medical help. Always remember to use only cold to luke warm water (never
more than 100 degrees F.). Hot water may cause more damage than good when
flushing. Eyes should be flushed for at least fifteen minutes (sometimes
longer depending on the situation) and a medical professional should always
double check for any consequential damage.
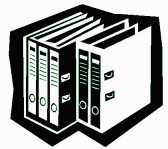
Material Safety Data Sheets (MSDS) are literature that manufacturers are required to create for each chemical or substance that they produce. To make things consistent
for consumers, each sheet is broken down into nine or ten sections depending on applicable situations:
The first section is always the Product Identification.
This section includes chemical and common names of ingredients which contribute to known health hazards or physical hazards and the common name of the mixture itself.
The second section lists Hazardous Ingredients.
The third section contains Physical Data.
This section usually includes physical and chemical characteristics of the hazardous chemical such as vapor pressure, flash point, and similar data.
Section four contains Fire and Explosion Hazard Information.
This section includes the physical hazards of the hazardous chemical, including the potential for fire, explosion, and reactivity to things.
Section five advises the consumer of Health Hazard Data.
This section lists the health hazards of the hazardous chemical, including signs and symptons of exposure, and any medical conditions which are generally recognized as being aggravated by exposure to the chemical. This section or a seperate section may indicate primary routes of entry into the body.
Section six specifies Reactivity Data.
This section will include the OSHA permissible exposure limit, the ACGIH Threshold Limit Value, and any other exposure limit used or recommended by the chemical manufacturer.
Section seven addresses Spill and Leak Procedures.
Section eight identifies Safe Handling and Use Information.
This section lists any generally applicable precautions for safe handling and use which are known to the chemical manufacturer including appropriate hygienic practices, protective practices, protective measures during repair and maintenance of contaminated equipment, and procedures for clean-up of spills and leaks.
Section nine refers to Special Precautions.
This section will identify any generally applicable control measures which are known to the chemical manufacturer such as appropriate engineering controls, work practices, and special personal protective equipment.
Section ten may refer to Transportation Issues, especially if a substance is considered hazardous in any way.
Other important information may include:
Emergency and first aid procedures;
The date of preparation of the material safety data sheet or the date of last revision;
The name, address, and telephone number of the chemical manufacturer, importer, or distributors who can provide additional information on the hazardous chemical and appropriate emergency procedures, should additional information be needed.
The preceding list is required by law to be on every MSDS for every liquid and chemical produced (as well as other types of products). Other information may be added as appropriate. The purpose is that every consumer or user can quickly become knowledgeable of products in time of crisis. MSDS are located in Housekeeping Closets, at Nursing Stations, in Maintenance Shops, in Dietary, and in areas where employees can gain quick access to the right information as needed. All departments that utilize chemicals or drugs should have their own sets of MSDS available and accessible to their employees. A sample Hazard Communication Procedure is outlined below.
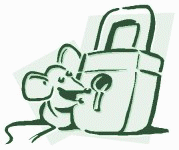
Lockout - Tagout Equipment is specific types of locks and tags used by Maintenance personnel which is designed to shut down electrical equipment, water lines, boiler pipes, gas lines, steam pipes, and other types of supply lines and or equipment controls at times when service is being performed. Too many injuries and deaths have been attributed to either not shutting down equipment or some unaware operator turning on equipment in the middle of service. An example would be an electrician repairing a 480 volt electrical motor, then some unaware operator turns the motor on, thus accidentally electrocuting the maintenance worker. Lockouts lock the electrical supply in the off position so that only the maintenance worker has the key. The tagouts tell all fellow employees that service work is in progress, so that they leave that piece of equipment untouched until work has been completed. All employees need to learn to recognize these special locks and tags and to learn how to work around the slight inconveniences that these lockouts may cause. A sample procedure is outlined below.
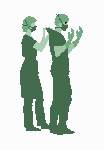
Personal Protective Equipment (PPE) are safety precautions designed to prevent bodily injury and the spread of dangerous disease Universal Precaution Procedures fall under this category. These precautions include, but are not limited to, gloves, goggles, face masks, hair nets, gowns, boots, protective lead shielding, and in some cases full body suits. Depending on the nature and properties of the hazard being handled, these special precautions lower or eliminate the risks involved. Employees are supposed to be fully trained prior to any dealings with inherent job hazards. This includes a full explanation as to what the risks are and what type of equipment is required to minimize those risks. Employers ultimately have responsibility to provide the appropriate protective equipment.
Blood Spill Kits and Mercury Spill Kits are specially designed materials and procedures to clean up each of these specific types of spills in a way that will not spread any known infection or poison to the cleaner or those in the immediate area. These kits are designed to be used in a certain manner. They should not be utilized by untrained, unfamiliar staff. If a blood spill or mercury spill occur, employees should notify and seek help from experienced fellow staff members. It is important to remember that mishandling certain types of spills, such as blood or mercury could potentially cause harm to the individual, and in some cases to those in close proximity.
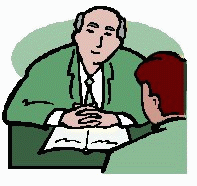
Incident Reports must be filled out and maintained regardless of how serious or how minor an accident may seem. It is important to keep track of all safety related incidents. These reports are normally filled out by an immediate supervisor, but can also be initiated by a shift supervisor, or even the employee if situations make supervisors unavailable. These reports help to analyze why accidents occur and what can be done to prevent similar circumstances. OSHA requires that a Master Log be maintained and posted during specific periods of the year. This allows statistics to be calculated and give us measurements from which to evaluate how our policies and procedures regarding safety are working or not working in the real world.
References:
BNA' s Safety Library on CD, Copyright 1994-1999, The Bureau of National Affairs, Inc.
OSHA Compliance, Copyright 1998-2000, SINGLBK's Web Page, Authored by Bob Singer, LNHA.
The Author's Own Notes And Field Experiences, 1980 - 2000.
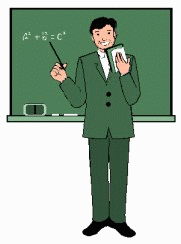
Sample Simplified Hazard Communications Program
Introduction:
The Hazard Communication Program is based on the concept that employees both need and have a right to know the hazards of the chemicals that they may have exposure during the course of their workday. They also have the need and right to know what protective measures are available to prevent adverse effects from occurring. This Facility's Hazard Communication Program is designed to provide employees with that information. When employees have information about the chemicals and hazards of their work environment, they can initiate steps to reduce exposures, substitute less hazardous materials (when possible), and establish proper work practices. It is intended that these combined efforts can help prevent the occurrence of work related illnesses and injuries caused by these hazards.
Description:
The major components of our Hazard Communications Program will include this written description of our program, labels and signs used for purposes of warning, general information, collection and posting of chemical material safety data sheets, and employee Inservice training. This Hazardous Communications Program will be a continuous program for this facility. Department Managers will be responsible for both initial and ongoing activities that will need to be undertaken to comply with the rules of this program. Additional support will be given in the way of general facility Inservice programs, which shall be intended to provide industry standards and procedures.
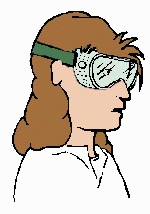
Hazardous Chemicals:
Hazardous chemicals will-be listed, posted, and made available to all employees during all work shifts and operating hours. These Material Safety Data Sheets will-be maintained as a group at one specific area in ____________________. Additional information may-be kept on file in specific Departments as determined appropriate by individual Department Managers. Lists of Department Managers will-be kept current through Administration and through related postings to each nursing wing.
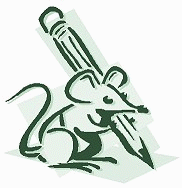
Labeling:
All Departments will maintain labels or create labels in absence of the original label to identify the contents within. Labels will be legible and prominently displayed. Persons responsible for ensuring labeling of all hazardous materials will-be the manager of each department. Labels will-be monitored continuously. When labels become no longer legible, they will-be redone to comply with this procedure. Factory labels and labels distributed with product will be the preferred method of labeling. Hand written labels will-be implemented as an acceptable substitute when preferred labels are not available.
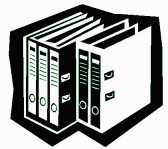
Material Safety Data Sheets:
Material Safety Data Sheets will-be maintained for each hazardous material used in performance of routine operations. These information sheets will-be supplied by either distributors of each product or the product's manufacturer. Product information will be available to all employees as listed above. Department Heads will be responsible for obtaining information and getting that information to the facility's central location and into the appropriate binder for employee reference.
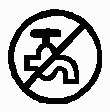
Signs:
Signs will be posted when operations create hazards for employees and or the general public, or as indicated in routine operational procedure instructions for particular tasks. Signs will be labeled to communicate the general nature of the hazard or that caution should be exercised. Examples include such things as posting of "Caution, Wet Floor" signs during mopping of dirty floors.
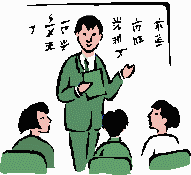
Employee Training:
Employees will-be trained on work related hazards through a combination of means to include, but not limited to, initial training and orientation, on the job instruction, and continuing industry standard Inservice programs. Information regarding specific hazards and recommended protective equipment will be made available through container labeling, Material Safety Data Sheets, and through Inservices on industry standards. Universal Precaution is an emphasized standard for this facility.
Training will-be provided by Department Heads or assigned staff representatives, Staff Inservice Coordinators, Personnel Managers, and Outside Instructors as determined by Administration.
Hazard Assessments:
Hazards, risks, and methods associated with non routine tasks will be assessed by Department Managers at time task is created. Department Managers will be responsible to train and direct all affected employees with regard to all practices set forth in this document.
References:
BNA' s Safety Library on CD, Copyright 1994-1999, The Bureau of National Affairs, Inc.
OSHA Compliance, Copyright 1998-2000, SINGLBK's Web Page, Authored by Bob Singer, LNHA.
The Author's Own Notes And Field Experiences, 1980 - 2000.
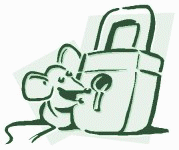
Sample Lockout / Tagout Procedures
Introduction:
The purpose of this procedure is to cover the servicing and maintenance of facility equipment in which the unexpected energization or start up of that equipment, or the release of stored energy from that equipment, could cause injury to employees. This procedure establishes a minimum level of safety requirements for the controls of such hazardous energy.
This procedure is designed to control the flow of energy during servicing and / or maintenance of that equipment. It has been edited down from regulations specified in 29 CFR 1910.147, The Control of Hazardous Energy, better known as Lockout / Tagout. It has been simplified into a more operational procedure that can be read, understood, and followed by all levels of employees. The following information has been edited from The Bureau of National Affairs, Inc., Safety Library on CD, their translation of this OSHA regulation and combined with the author's own understanding and interpretation from seminars, web pages, inspections, and practice in the field of Nursing Home Safety Issues.
This procedure is also designed to provide instruction and insight to affixing appropriate lockout devices and tagout devices to energy isolating devices. This procedure will help to otherwise disable equipment to prevent unexpected energization, startup, or release of stored energy in order to prevent injury to employees.
Description of Procedures:
If an energy-isolating device is not capable of being locked out, The Facility's Energy Control Program shall utilize a tagout system.
If an energy-isolating device is capable of being locked out, The Facility's Energy Control Program shall utilize a lockout, unless it can be substantiated that the utilization of a tagout system will provide full employee protection.
This procedure is to be followed whenever replacement, major repair, renovation, or modification of equipment is to be performed. For new equipment that is installed, the energy isolating devices for such equipment shall be designed to accept a lockout device.
When a tagout device is used on an energy-isolating device and is capable of being locked out, the tagout device shall be attached at the same location that the lockout device would have been attached. The Facility's Maintenance Supervisor shall double check that the tagout program will provide a level of safety equivalent to that obtained by using a lockout program.
Additional safety measures such as the removal of an isolating circuit, blocking of a controlling switch, opening of an extra disconnecting device, or the removal of a valve handle, in order to reduce the likelihood of inadvertent energization, shall be done as discretion warrants.
Specific procedures for shutting down, isolating, blocking, and securing machines or equipment to control hazardous energy will be described later in this document.
Specific procedures for the placement, removal, and transfer of lockout devices or tagout devices and responsibilities for them will be described later in this document.
Specific requirements for testing equipment to determine and verify the effectiveness of locked out devices, tagout devices, and other energy control measures will be described later in this document.
Locks, tags chains, wedges, key blocks, adapter pins, self-locking fasteners, or other hardware will be provided by The Facility's Maintenance Department for isolating, securing, or blocking equipment from energy sources.
Lockout devices and tagout devices shall be singularly identified as the only the devices used for controlling energy. They shall not be used for other purposes.
All lockout and tagout devices shall be capable of withstanding the environment to which they are exposed for the maximum period of time that exposure is expected.
Tagout devices shall be constructed and printed so that exposure to weather conditions, such as wet and damp locations, will not cause the tag to deteriorate or the message on the tag to become illegible.
Lockout and tagout devices shall be standardized within the facility in at least one of the following criteria: color, shape, or size.
Lockout devices shall be substantial enough to prevent removal without the use excessive force or unusual techniques.
Tagout devices and their means of attachment shall also be substantial enough to prevent inadvertent or accidental removal.
Lockout devices and tagout devices shall indicate the identity of the employee applying the device(s).
Tagout devices shall warn against hazardous conditions if the machine or equipment is energized and shall include wording such as, "DO NOT START", "DO NOT OPEN", "DO NOT ENERGIZE", "DO NOT OPERATE", "DO NOT USE", or similar appropriate instructions.
The Facility's Department Managers will review energy control procedures for their Departments at least annually to ensure that requirements and procedures are being followed and that they remain appropriate to any facility upgrades or changes that may have occurred. Changes to policies will be made if determined to correct any inadequacies that were identified. Documentation will be maintained to certify that these procedures were reviewed by inserting a date, name, title, and signature of reviewer on the cover page.
Training and Continuing Education:
The Facility's Management Team and Staff Inservicers will provide training to ensure that the purpose and function of the energy control program are understood by employees and that the knowledge and skills required for the safe application, usage, and removal of the energy controls are acquired by those employees.
Training shall include recognition of applicable hazardous energy sources, the type and magnitude of the energy available in the workplace, and the methods and means necessary for energy isolation and control.
All employees will be instructed the purpose and use of the Energy Control procedure. Each employee whose work operations are or may be in an area where Energy Control procedures may be utilized shall be instructed about the procedure and about the prohibition relating to attempts to reenergize equipment which are locked out or tagged out.
Employees will be trained that when a lockout or tagout is attached to an energy isolating means, it is not to be removed without authorization of the authorized person responsible for it. It is never to be bypassed, ignored, or otherwise defeated.
Employees will be trained and retrained whenever there is a change in their job assignments, a change in equipment, a change in processes that present a new hazard, or when there is a change in the Energy Control procedures.
Additional retraining shall be conducted whenever the employer has reason to believe that there are deviations from, or inadequacies, in the employee's knowledge or use of the Energy Control procedures.
Training will be directed towards the intention that employees establish proficiency and understanding of new or revised control procedures. The Facility's Department Managers shall certify that employee training has been accomplished and or kept up to date by documenting employee's name and date from each training. This may be accomplished by using standard Inservice Sign-In forms.
Specific Procedures for Shutting Down Equipment:
1. Each new or transferred employee whose work operations are or may be affected will be instructed in the purpose and use of the lockout or tagout procedures.
2. In preparation for shutdown, before an authorized or affected employee turns off the piece of equipment, the authorized employee shall investigate and gather knowledge of the type and magnitude of the energy, the hazards of the energy to be controlled, and the method or means to control that energy. All affected employees will be notified that the lockout or tagged out system is going to be utilized and the reason therefor. The authorized employee shall determine which electrical switch or which mechanical valves will be shutdown to
leave the unit disabled and deenergized.
3. The equipment shall be turned off or shut down using the procedures and devices specifically designed for that equipment. An orderly shutdown will be conducted to avoid any increased hazards to employees as a result of the equipment stoppage. A switch, valve, or other energy-isolating device will be operated so that the equipment is isolated from its energy source. Stored energy such as hydraulic fluids, air pressure, gas pressure, steam pressure, water pressure, electric power, etc., will be dissipated, restrained, bled off, or otherwise blocked to prevent injury to employees.
4. The Maintenance Staff will assist and or perform services to locate and identify all isolating devices. They will be responsible to make certain which switches, valves, or other isolating devices apply to the equipment to be locked or tagged out. These devices, as determined, shall be physically located and operated in such a manner as to isolate the machine or equipment from its energy sources.
5. An authorized employee shall affix lockout and or tagout devices to each energy-isolating device. Multiple locks or tags will be used in cases that involve more than one individual or more than one department.
6. Lockout devices where used shall be affixed in a manner that will hold the energy isolating devices in a "safe" or "off" position.
7. Tagout devices, where used, shall be affixed in such a manner that they will clearly indicate that the operation or movement of energy isolating devices from the "safe" or "off" position is prohibited.
8. Where the tagout devices are used with energy isolating devices, designed with the capability of being locked, the tag attachment shall be fastened at same point at which the lock would have been attached.
9. Where a tag cannot be affixed directly to the energy isolating device, the tag shall be located as close as safely possible to the device in a position that will be immediately obvious to anyone attempting to operate that device.
10. Prior to starting work on equipment that have been locked out or tagged out, the authorized employee shall verify that isolation and deenergization of the equipment have been accomplished. After ensuring that no personnel are exposed, and as a double-check, after all potentially hazardous stored or residual energy is relieved, disconnected, restrained, or otherwise rendered safe, the authorized employee shall operate the push button and or other normal operating controls to make certain that the equipment will not operate. Be
sure to return the operating controls to a "neutral" or "off" position after the test sequence is completed.
Specific Procedures for Restoring Equipment Back to Service:
Before lockout or tagout devices are removed and energy is restored to equipment, the following procedures and actions should be taken by the authorized employees:
1. After the servicing is complete and equipment is ready to return to normal production operations, the work area shall we inspected to ensure that all nonessential items have been removed. Check to ensure that equipment components are operationally in tact. The work area shall also be checked to ensure that all employees have been safely positioned or removed.
2. Make sure to reinstall all safety guards. Remove all tools from machine or equipment. Then remove all lockout and tagout devices.
3. After lockout and tagout devices have been removed and before a machine or equipment is started, all affected employees shall be notified that the lockout and tagout devices have been removed and that the equipment start up processes are about to begin.
4. Operate the energy isolating devices to restore energy to the equipment.
Procedures for Contractors and Multiple Lockouts:
Whenever outside servicing personnel are to be engaged in activities covered by the scope and application of this procedure, the on-site facility representative and outside contractor shall inform each other of their respective lockout and tagout policies and procedures. The on-site facility representative shall ensure that his / her employees understand and comply with the restrictions and prohibitions of the outside contractor's Energy Control Program.
When more than one individual is required to lockout or tagout equipment, each shall place his/her own personal lockout or tagout device on the energy isolating devices.
When the energy isolating devices cannot accept multiple locks or tags, a multiple lockout or tagout device (hasp) should be used. If lockout is used, a single lock may be used to lockout machine or equipment with that being placed in a lockout box / cabinet which allows the use of multiple locks to secure it. Each employee will then use his/her own lock to secure the box / cabinet. As each person no longer needs to maintain his / her lockout protection, that person will remove his or her lock from the box / cabinet.
When service is performed by a crew, multiple departments, or some other type of group, they shall utilize a procedure similar to that before mentioned, which will afford all employees a level of protection equivalent to that provided by the implementation of a personal lockout or tagout device.
Primary responsibility for safety will be vested in an authorized employee or Department Head for a number of employees working under the protection of a group lockout or tagout device.
Each authorized employee shall affix a personal lockout or tagout device to the group lockout device, group lock box, or compatible mechanism when he / she begins work, and shall remove those devices when he / she stops working on the machine or equipment being serviced.
Communication procedures shall be utilized during shift or personnel changes to ensure that there is continuity of lockout and tagout protection. This includes provision for the orderly transfer of lockout and tagout device protection between offing and oncoming employees. The purpose of this is to minimize exposure to hazards from the unexpected energization or startup of the machine or equipment, or the release of any stored energy.
In Summary:
The purpose of Lockout and Tagout Procedures is to protect all facility staff from unnecessary injury caused from unintentional accidents. A few basic rules can be followed and these accidents can be avoided. This makes the workplace safer for all of us. So, please notice, understand, and obey the warnings!
References:
BNA' s Safety Library on CD, Copyright 1994-1999, The Bureau of National Affairs, Inc.
OSHA Compliance, Copyright 1998-2000, SINGLBK's Web Page, Authored by Bob Singer, LNHA.
The Author's Own Notes And Field Experiences, 1980 - 2000.
Copyright 1996, Revised 1999, 2001 By Bob Singer, BS, NHA, PCHA, Author.
Alzheimer's
Outreach http://alzheimers.zarcrom.com
Bob's Email
Click
HERE to go back